前言
目前,塑膠製品得到了越來越廣泛的應用,塑膠的成型方法也越來越多,如注射成型、擠壓成型、真空成型、發泡成型、中空吹塑成型、薄膜吹塑成型,以及熱固性塑料的各種成型等。其中,塑料的注射成型是最主要的成型方法,塑料注射模則是注射成型的工具。
注塑模具是一種生產塑料製品的工具。它由幾組零件部分構成,這個組合內有成型模腔。注塑時,模具裝夾在注塑機上,熔融塑料被注入成型模腔內,並在腔內冷卻定型,然後上下模分開,經由頂出系統將製品從模腔頂出離開模具,最後模具再閉合進行下一次注塑,整個注塑過程是循環進行的。
下面將主要介紹塑料注射模具設計的相關知識。
塑膠模具設計準則
1.
單向流動:保證在填充過程中,塑料應該在一個方向上流動 ,並且保持一個直的流動前沿。這導致單方向定位的產生。
2. 流動平衡:所有的流動路徑應該是平衡的,即在相同時間以相同壓力進行充填 。
3. 恆定壓力梯度:最有效率的填充方式是壓力梯度 (壓力降低對單位長度) 沿著流動路徑是固定的時候。
4. 最大剪應力:剪應力在填充的時候應該是小於材料臨界的最大剪切應力,數值依賴於材料和應用。
5. 熔接/融合位置:在最不敏感部位放置熔接和融合線 。
6. 避免滯留:盡可能避免在流體流動路徑分為厚的和薄流動路徑那裏設置澆口。
7. 避免潛流:通過澆口的設置避免潛流,保證流體在最後充填區相遇。
8. 可控制的磨擦加熱:人為控制的磨擦加熱設計流道,
增加型腔熔體溫度,這將在產品中獲得較低的應力,不會因塑料長期處於較高的溫度而引起塑料的降解。
9. 流道熱閥:利用熱閥設計流道系統, 保證澆口凍結時型腔剛好充填完畢和充分保壓,避免在模具充填完畢後過保壓或產生倒流。
10. 流道/型腔比:為高壓力降設計流道系統, 使流道材料最小獲得一個低比率的流道/型腔設計。
模具設計時的注意事項
塑料注射模具是成型塑料製品的主要工具,而一般說來塑料製品通常是批量和大批量生產,因此要求塑料模具在使用時應具有高效率、高質量及成型後少加工或不加工,所以在模具設計時就必須考慮這些問題:
1.
根據塑件的使用性能和成型性能,確定簡潔合理的分型面基準面和澆口的位置等形式,這是在模具設計中較為重要的問題。
2.
在設計模具時應注意它在製造過程中的工藝性,根據工廠實際設備狀況以及技朮力量等客觀因素,制定出立足本地切實可行的設計方案,從整體到零件都能易於加工,易於保証尺寸精度。
3. 應充分考慮注射過程中的生產效率,即在單位時間內提高注射次數,也就是縮短成型週期。
4.
綜合塑件的結構狀況,盡可能地將需要有精度要求的尺寸以及孔、柱、凸、凹等結構全部在模具中表現出來,即成型的塑件應該是不需要或不太需要事後加工的較完整的塑件。
5. 模具結構力求簡單適用、穩定可靠,縮短製造週期和降低製造成本,並應便於裝配,便於維修和便於更換易損件等。
6.
重視模具材料的選擇與處理,在模具結構件間或與模體與塑件間在頂出過程中有頻繁接觸和磨擦的部位,零件件應選擇優質鋼材及必要的熱硬處理,使結構零件提高耐磨性及強度,以減少故障,提高模具壽命。
7.
模具的標準化生產也是模具設計中應該考慮的問題。由於塑件的結構各式各樣,模具的型腔、型芯也各不相同,但模體選用標準模架、常用頂桿、導向零件、澆口套等都可以晝量採用標準件。
塑料注射模具的基本結構
根據注射模的功能及作用,大體由以下幾部分組成:
1.
熔融物料從注射機嘴流入模腔的澆注系統,如主流道、分流道、澆口、冷井及鉤料桿等。
2. 塑件成型零件,如型芯、型腔以及其它輔助件等。
3. 調節模具溫度的溫控系統,如加熱管,發熱線等。
4.
從模具把塑件脫出的頂出系統:側分型機構以及頂出時必須採用的二次頂出機構、頂出系統的先復位機構和為實現順序分型所必須採用的順序定距分型機構
5. 把模體可靠地安裝在注射機上的安裝部分,如工字板,碼模坑。
6. 將各結構件組成整體的連接系統。
7. 保証各結構件相互的移動精度的導向系統,如導柱及導滑槽等。
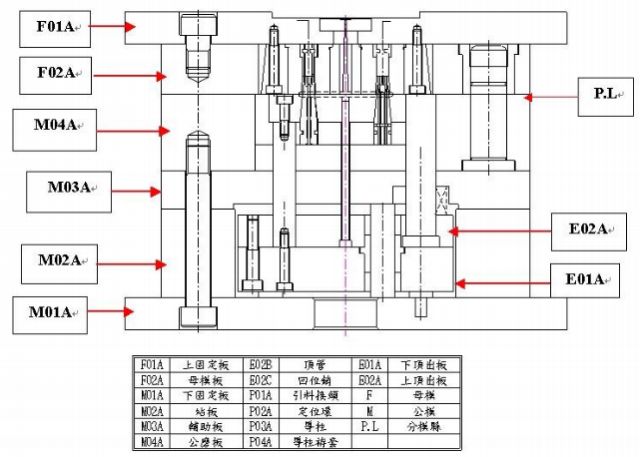
塑膠模具的分類
根據澆注系統形式的不同可將模具分為三類:
1.
大水口模具:流道及澆口在分模線上,與產品在開模時一起脫模,設計最簡單,容易加工,成本較低,所以較多人採用大水口系統作業。
2.
細水口模具:流道及澆口不在分模線上,一般直接在產品上,所以要設計多一組水口分模線,設計較為複雜,加工較困難,一般要視產品要求而選用細水口系統。
3.
熱流道模具:此類模具結構與細水口大體相同,其最大區彆是流道處於一個或多個有恆溫的熱流道板及熱唧嘴裏,無冷料脫模,流道及澆口直接在產品上,所以流道不需要脫模,此系統又稱為無水口系統,可節省原材料,適用於原材料較貴、製品要求較高的情況,設計及加工困難,模具成本較高。
設計事例研究
一、設計準備
1. 必需的圖紙、金型仕樣書的內容等的確認。
2. 把握圖面的概要。
部品圖決定了金型設計的最終目的,必須透徹地理解。本廠的部品圖是採用第三角法繪製的,通常由以下部分構成:
正面圖、平面圖、側面圖、斷面圖、詳細圖、參考圖、註記、公差一覽、仕上記號一覽、標題欄等。
在視圖過程中要注意以下方面:
a. 公差要求較嚴格處;
b. 對金型構造有影響的部位;
c. 現有圖面無法理解的部分;
d. 註記中特彆突出的事項﹔
e. 特殊的材料和熱處理要求;
f. 部品壁厚較薄處(t<0.6mm)﹔
g. 部品壁厚較厚處;
h. 外觀上有無特彆仕樣要求。
3. 註記部分的檢討
a. 澆口種類、位置、數量
b. 入子分割線的要求:由於入子分隔線會在製品表面形成接痕,影響外觀,尤其對折疊部位有害,所以設計者應遵守部品圖的規定。
c. 成型品表面劃傷等缺陷的規定
d. 未注公差的要求。
如圖面提供的資料不全,需跟產品工程師聯繫,取得全部資料。
使用彩筆標記出自己認為較重要的,以利於下一步的設計。
二、成型品基本圖的設計
1.
下面是塑膠模具設計的大致流程:初期檢討→成型品基本圖設計→金型構造設計→部品圖設計→檢圖→出圖
2. 下面就成型品基本圖的設計手法進行講解:
a. 瞭解成型材料的特性
最關鍵的是流動性能的好壞和收縮率的大小
b. 可充填性的檢討
應全面考慮以下幾個方面:
(1) 型腔可否完全填充;(2) 溶接痕的位置;(3) 氣泡的發生;(4) 成型品的變形;(5) 點澆口的切斷痕;(6)
其他
3. 澆口位置的確定
4. 澆口形狀的確定
5. 分型面的確定
應參照下述原則:(1) 盡量採用平面;(2) 易於加工;(3) 無離型不良發生;(4) 外觀上分割線無影響處
6. 拔模斜度的決定(固定側)
為防止離型不良,有必要在固定側型芯處設置拔模斜度,但要在成型品公差範圍內,一般以30』~3°為宜。
7. 拔模斜度的決定(可動側)
如有必要,可動側也可加拔模斜度,但一般可不加。如有頂出不良,可通過加裝頂桿的方法來解決。
8. 頂桿的配置
按照以下原則:
a. 頂出面積盡可能大,因細小的頂桿孔難以加工。
b. 盡量採用圓頂桿,因方頂出孔難以加工(但利用鑲件分割線做出的較簡單)。
c. 頂桿要配置在型芯附近。
d. 頂桿孔周圍最小1mm壁厚保證。
三、金型構造設計
成型品基本圖完成以後,即可開展最重要的工作-金型構造圖面的設計。這部分工作占金型設計全部研討工作的80%。下面就是具體的設計流程:
1. 成型機金型取付仕樣的確認:
a. 滑桿間距的確認
金型大小不可超過滑桿間距,通常要留20mm以上的安全距離。
b. 最小型厚的確認
金型的型厚要大於注射機的最小型厚
c. 最大開模行程的確認
d. 最大鎖模力的確認
e. 理論射出容量的確認
f. 定位圈直徑的確認(以選擇定位圈型號)
g. 注射機噴嘴先端形狀的確認(以選擇澆口套型號)
h. 最大型厚的計算
T=最小型厚+最大開模距離-S1-S2-S
2.
型腔配置方法的檢討:對於多型腔模具而言,要妥善安排型腔位置,使之投影中心完全位於模架中心上,並使流道最短地達到均衡進料。
3. 型腔壁厚度的確定
4.
模架的選擇對於塑料注射模具而言,模架均已標準化。在選擇模架時,除了大小規格外,應確認以下方面:
a. 導柱導套的位置,有的導柱在固定側,而有的在可動側。根據需要來選擇。
b. 對於各模板的厚度,應結合成型品基本圖來確認。一般來說,要使鑲件非成形部分的長度在30mm左右為宜。
四、部品圖設計
在進行構造設計完成以後,根據成形品基本圖和金型構造圖進行金型部品圖設計,包括下述內容:
a、設計需加工的部品圖面。
b、外構件追加工部品圖面。
c、購入部品仕樣書。
1. 型腔部分的設計:
a. 從金型構造圖中把型腔部分的外形提取出來。X-Y方向與模板嵌合,注意公差與配合。Z方向採用螺釘或掛鉤或鍵固定均可。
b. 成形部分形狀與寸法
c. 型芯均採用掛鉤的形式與型腔件配合,X-Y方向用公差來嚴格控制。
d. 澆口設計
e. 固定方法
f. 材質、硬度的決定
2. 固定側型芯的設計:形狀與寸法根據成形品基本圖確定。
3.
可動側型芯、型腔設計大致與固定側相同,但多出頂出部分的設計內容。
五、檢圖
部品圖設計完了以後要進行檢圖,這與設計工作同等重要。在投入生產前發現錯誤,要比在生產中或完成後才發現要節省大量的金錢與精力。
檢圖工作,可由設計者自身承擔,也可由第三者擔任。在檢圖中應把握如下原則:
a. 詳細設計、重要設計檢查時,最好在精力充沛時進行。
b. 連續工作1~2小時,應休息10~15分鐘,保持頭腦清醒。
c. 不要懼怕失敗,在失敗中取得成長的經驗。
d. 不要從詳細設計著手,應從總體方案開始,這樣容易發現大的原則性的錯誤。
e. 可調查類似金型在使用過程中發生的問題,並與自己的設計工作相對照。 |